Instrumentação Industrial Pressão: Como Garantir Precisão e Eficiência em Processos Industriais
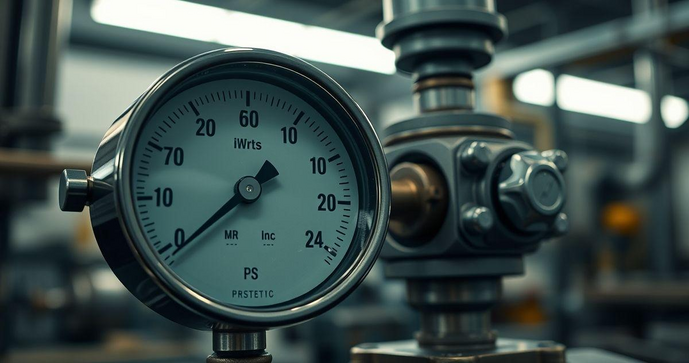
Por: Redator - 21 de Março de 2025
A instrumentação industrial pressão desempenha um papel crucial na automação e controle de processos em diversas indústrias. Com a necessidade crescente de precisão e eficiência, entender os diferentes tipos de sensores de pressão e suas aplicações se torna fundamental. Este artigo abordará a importância da instrumentação de pressão, os tipos disponíveis no mercado, além de práticas de manutenção e as últimas tendências do setor.
Importância da Instrumentação Industrial Pressão na Indústria
A instrumentação industrial pressão é um componente vital em diversos setores, incluindo petroquímico, farmacêutico, alimentício e de energia. A precisão na medição da pressão é essencial para garantir a segurança, eficiência e qualidade dos processos industriais. A seguir, discutiremos a importância da instrumentação de pressão e como ela impacta diretamente a operação das indústrias.
Um dos principais motivos pelos quais a instrumentação industrial pressão é tão importante é a segurança. Em muitas indústrias, a pressão inadequada pode levar a acidentes graves, como explosões ou vazamentos de substâncias perigosas. Por exemplo, em refinarias de petróleo, a pressão deve ser monitorada constantemente para evitar situações de risco. Sensores de pressão bem calibrados e sistemas de monitoramento eficazes ajudam a garantir que os níveis de pressão permaneçam dentro dos limites seguros, protegendo tanto os trabalhadores quanto o meio ambiente.
Além da segurança, a instrumentação de pressão também desempenha um papel crucial na eficiência operacional. Processos industriais muitas vezes dependem de condições específicas de pressão para funcionar corretamente. Por exemplo, em sistemas de aquecimento, a pressão do vapor deve ser mantida em níveis ideais para garantir a transferência de calor eficiente. Se a pressão estiver muito baixa, o sistema pode não funcionar de maneira eficaz, resultando em desperdício de energia e aumento de custos operacionais. Por outro lado, uma pressão excessiva pode causar danos aos equipamentos e aumentar o risco de falhas. Portanto, a instrumentação de pressão é fundamental para otimizar o desempenho dos sistemas industriais.
A qualidade do produto final também está intimamente ligada à instrumentação industrial pressão. Em indústrias como a alimentícia e farmacêutica, a pressão deve ser controlada com precisão para garantir que os produtos atendam aos padrões de qualidade e segurança. Por exemplo, na produção de alimentos enlatados, a pressão durante o processo de esterilização deve ser monitorada para garantir que todos os microrganismos sejam eliminados, evitando contaminações. A instrumentação de pressão, portanto, não apenas assegura a segurança, mas também contribui para a consistência e qualidade dos produtos.
Outro aspecto importante da instrumentação industrial pressão é a conformidade regulatória. Muitas indústrias são obrigadas a seguir normas e regulamentos rigorosos que exigem monitoramento e controle precisos da pressão. A não conformidade pode resultar em penalidades financeiras e danos à reputação da empresa. Portanto, investir em sistemas de instrumentação de pressão adequados é essencial para garantir que as operações estejam em conformidade com as regulamentações do setor.
Além disso, a instrumentação de pressão é fundamental para a automação industrial. Com o avanço da tecnologia, muitos processos industriais estão se tornando cada vez mais automatizados. Sensores de pressão conectados a sistemas de controle permitem que as empresas monitorem e ajustem automaticamente as condições de operação em tempo real. Isso não apenas melhora a eficiência, mas também reduz a necessidade de intervenção manual, minimizando o risco de erro humano.
As inovações tecnológicas também têm impulsionado a importância da instrumentação industrial pressão. Novos sensores e dispositivos de medição estão sendo desenvolvidos para oferecer maior precisão, confiabilidade e facilidade de uso. Por exemplo, sensores de pressão sem fio estão se tornando cada vez mais populares, permitindo que os dados sejam transmitidos em tempo real para sistemas de controle centralizados. Isso facilita a análise de dados e a tomada de decisões informadas, melhorando ainda mais a eficiência operacional.
Por fim, a instrumentação industrial pressão é um elemento essencial para a sustentabilidade. Com a crescente pressão para reduzir o consumo de energia e minimizar o desperdício, as indústrias estão cada vez mais focadas em otimizar seus processos. A instrumentação de pressão desempenha um papel crucial nesse esforço, permitindo que as empresas monitorem e ajustem suas operações para reduzir o consumo de recursos e minimizar o impacto ambiental.
Em resumo, a instrumentação industrial pressão é fundamental para garantir a segurança, eficiência, qualidade e conformidade nas operações industriais. Com a evolução da tecnologia e a crescente demanda por processos mais sustentáveis, a importância da instrumentação de pressão só tende a aumentar. Para mais informações sobre como a instrumentação pode beneficiar sua operação, consulte o guia completo sobre Instrumentação industrial .
Tipos de Sensores de Pressão e Suas Aplicações
Os sensores de pressão são dispositivos fundamentais na instrumentação industrial, utilizados para medir a pressão de gases e líquidos em uma variedade de aplicações. A escolha do tipo de sensor adequado é crucial para garantir a precisão e a eficiência dos processos industriais. Neste artigo, exploraremos os principais tipos de sensores de pressão e suas aplicações em diferentes setores.
Um dos tipos mais comuns de sensores de pressão é o sensor piezoelétrico. Este sensor utiliza materiais piezoelétricos que geram uma carga elétrica quando submetidos a uma pressão. Os sensores piezoelétricos são altamente sensíveis e são frequentemente utilizados em aplicações que requerem medições rápidas e precisas, como em testes de pressão em laboratórios e em equipamentos de monitoramento de pressão em tempo real. Eles são ideais para medir pressões dinâmicas, como em sistemas hidráulicos e pneumáticos.
Outro tipo amplamente utilizado é o sensor de pressão resistivo, que funciona com base na variação da resistência elétrica de um material quando submetido a pressão. Esses sensores são conhecidos por sua robustez e confiabilidade, sendo frequentemente utilizados em ambientes industriais adversos. Eles são comumente aplicados em sistemas de controle de processos, onde a precisão na medição da pressão é essencial para garantir a segurança e a eficiência operacional.
Os sensores de pressão capacitivos são outra categoria importante. Esses sensores medem a pressão com base na variação da capacitância entre duas placas condutoras. Quando a pressão é aplicada, a distância entre as placas muda, alterando a capacitância. Sensores capacitivos são conhecidos por sua alta precisão e estabilidade a longo prazo, sendo frequentemente utilizados em aplicações que exigem medições de pressão em ambientes controlados, como em laboratórios e indústrias farmacêuticas.
Os sensores de pressão de membrana são projetados para medir a pressão de líquidos e gases em contato direto com a membrana. Esses sensores são frequentemente utilizados em aplicações onde a pressão do fluido deve ser medida sem contaminação, como em processos alimentícios e farmacêuticos. A membrana atua como uma barreira, permitindo que a pressão seja medida sem que o fluido entre em contato com os componentes eletrônicos do sensor.
Além disso, os sensores de pressão de tubo Bourdon são uma opção tradicional e amplamente utilizada. Esses sensores utilizam um tubo curvado que se desdobra quando a pressão é aplicada, movendo um ponteiro em uma escala. Embora sejam menos precisos do que os sensores eletrônicos modernos, os sensores de tubo Bourdon são robustos e confiáveis, sendo frequentemente utilizados em aplicações industriais gerais, como em medidores de pressão de água e ar.
Os sensores de pressão digitais têm ganhado popularidade nos últimos anos devido à sua capacidade de fornecer leituras em tempo real e a facilidade de integração com sistemas de automação. Esses sensores geralmente possuem uma interface digital que permite a comunicação com sistemas de controle e monitoramento. Eles são amplamente utilizados em indústrias que exigem monitoramento contínuo da pressão, como na indústria petroquímica e em sistemas de HVAC (aquecimento, ventilação e ar condicionado).
Uma aplicação específica que merece destaque é a Calibração RBC , que envolve a calibração de sensores de pressão em fluxômetros. A calibração é essencial para garantir que os sensores estejam medindo a pressão com precisão, o que é fundamental para o desempenho adequado dos sistemas de medição de fluxo. A calibração regular dos sensores de pressão ajuda a evitar erros de medição que podem levar a ineficiências operacionais e problemas de segurança.
Os sensores de pressão também são utilizados em aplicações automotivas, como no monitoramento da pressão dos pneus e na medição da pressão do óleo do motor. Esses sensores são essenciais para garantir a segurança e o desempenho dos veículos, ajudando a prevenir falhas mecânicas e melhorando a eficiência do combustível.
Além disso, os sensores de pressão são amplamente utilizados em sistemas de monitoramento ambiental, onde são empregados para medir a pressão atmosférica e a pressão em sistemas de ventilação. Esses dados são cruciais para garantir a qualidade do ar e a eficiência energética em edifícios e instalações industriais.
Em resumo, a escolha do tipo de sensor de pressão adequado depende das necessidades específicas da aplicação. Cada tipo de sensor possui características únicas que o tornam mais adequado para determinadas situações. Compreender as diferenças entre os tipos de sensores de pressão e suas aplicações é fundamental para garantir a precisão e a eficiência dos processos industriais. A instrumentação de pressão é uma parte essencial da automação industrial, contribuindo para a segurança, eficiência e qualidade em diversas indústrias.
Manutenção e Calibração de Equipamentos de Pressão
A manutenção e calibração de equipamentos de pressão são processos essenciais para garantir a precisão e a confiabilidade das medições em sistemas industriais. Equipamentos de pressão, como sensores e manômetros, desempenham um papel crucial em diversas aplicações, desde a produção de energia até a fabricação de produtos químicos. A seguir, discutiremos a importância da manutenção e calibração, as melhores práticas e os benefícios de manter esses equipamentos em condições ideais.
A manutenção regular dos equipamentos de pressão é fundamental para evitar falhas e garantir que eles funcionem corretamente. Com o tempo, os sensores de pressão podem sofrer desgastes, contaminação ou descalibração, o que pode levar a medições imprecisas. A falta de manutenção pode resultar em custos elevados, interrupções na produção e até mesmo riscos à segurança. Portanto, implementar um programa de manutenção preventiva é uma estratégia eficaz para minimizar esses problemas.
Um dos principais aspectos da manutenção é a limpeza dos sensores e componentes associados. A sujeira, poeira e resíduos podem se acumular nos equipamentos, interferindo nas medições e causando falhas. É recomendável realizar limpezas regulares, utilizando produtos adequados que não danifiquem os componentes eletrônicos. Além disso, é importante verificar se há vazamentos nas conexões e nas tubulações, pois vazamentos podem afetar a pressão medida e comprometer a segurança do sistema.
A calibração é outro aspecto crítico na manutenção de equipamentos de pressão. A calibração é o processo de ajustar e verificar a precisão dos instrumentos de medição, garantindo que eles forneçam leituras corretas. A calibração deve ser realizada em intervalos regulares, de acordo com as recomendações do fabricante e as normas da indústria. A frequência da calibração pode variar dependendo do tipo de equipamento, das condições de operação e da criticidade das medições.
Existem diferentes métodos de calibração, e a escolha do método adequado depende do tipo de equipamento e da aplicação. A calibração pode ser realizada em campo ou em um Laboratório de Calibração . A calibração em campo é conveniente, pois permite que os técnicos verifiquem e ajustem os equipamentos diretamente no local de operação. No entanto, a calibração em laboratório geralmente oferece maior precisão, pois os equipamentos podem ser testados em condições controladas e com instrumentos de referência de alta precisão.
Durante o processo de calibração, é importante seguir um procedimento sistemático. Isso geralmente envolve a comparação das leituras do sensor com um padrão de referência conhecido. Se houver discrepâncias, o equipamento deve ser ajustado para garantir que as medições estejam dentro das especificações aceitáveis. Após a calibração, é fundamental documentar os resultados e manter registros precisos, pois isso pode ser necessário para auditorias e conformidade regulatória.
Além da calibração, a verificação do desempenho dos equipamentos de pressão deve ser realizada regularmente. Isso inclui testes de funcionalidade e a análise de dados históricos para identificar tendências ou padrões que possam indicar problemas. Se um sensor de pressão apresentar leituras inconsistentes ou fora do normal, isso pode ser um sinal de que ele precisa ser recalibrado ou substituído.
Os benefícios de uma manutenção e calibração adequadas são significativos. Primeiramente, a precisão das medições é garantida, o que é crucial para a segurança e eficiência dos processos industriais. Equipamentos de pressão bem calibrados ajudam a evitar falhas catastróficas, como explosões ou vazamentos, que podem resultar em danos materiais e riscos à vida. Além disso, a manutenção regular pode prolongar a vida útil dos equipamentos, reduzindo a necessidade de substituições frequentes e os custos associados.
Outro benefício importante é a conformidade regulatória. Muitas indústrias são obrigadas a seguir normas rigorosas que exigem a calibração regular de equipamentos de medição. A não conformidade pode resultar em penalidades financeiras e danos à reputação da empresa. Portanto, manter um programa de manutenção e calibração adequado não apenas garante a segurança, mas também ajuda a evitar problemas legais e financeiros.
Por fim, a manutenção e calibração de equipamentos de pressão são essenciais para a eficiência operacional. Equipamentos bem mantidos e calibrados funcionam de maneira mais eficiente, resultando em menos desperdício de recursos e maior produtividade. Isso é especialmente importante em indústrias onde a pressão e o controle de processos são críticos para a qualidade do produto final.
Em resumo, a manutenção e calibração de equipamentos de pressão são processos fundamentais para garantir a precisão, segurança e eficiência nas operações industriais. Implementar um programa de manutenção preventiva, realizar calibrações regulares e seguir as melhores práticas são passos essenciais para maximizar o desempenho dos equipamentos. Ao investir na manutenção e calibração, as empresas podem não apenas proteger seus ativos, mas também garantir a qualidade e a segurança de seus produtos.
Tendências e Inovações em Instrumentação Industrial Pressão
A instrumentação industrial pressão está em constante evolução, impulsionada por inovações tecnológicas e pela crescente demanda por eficiência e precisão nos processos industriais. As tendências atuais refletem a necessidade de sistemas mais inteligentes, conectividade e automação, que não apenas melhoram a eficiência operacional, mas também garantem a segurança e a conformidade regulatória. Neste artigo, exploraremos algumas das principais tendências e inovações na área de instrumentação de pressão.
Uma das tendências mais significativas é a integração da Internet das Coisas (IoT) na instrumentação industrial. Sensores de pressão conectados à IoT permitem que os dados sejam coletados e transmitidos em tempo real para sistemas de monitoramento centralizados. Isso possibilita que as empresas monitorem continuamente as condições de pressão, identifiquem anomalias e tomem decisões informadas rapidamente. A conectividade também facilita a manutenção preditiva, onde os dados históricos são analisados para prever falhas antes que elas ocorram, reduzindo o tempo de inatividade e os custos de manutenção.
Outra inovação importante é o desenvolvimento de sensores de pressão sem fio. Esses sensores eliminam a necessidade de fiação complexa, facilitando a instalação e a manutenção. Sensores sem fio são especialmente úteis em ambientes industriais onde o acesso a cabos pode ser difícil ou perigoso. Além disso, a tecnologia sem fio permite que os sensores sejam instalados em locais remotos, ampliando as possibilidades de monitoramento em áreas que antes eram inacessíveis.
A miniaturização dos sensores também é uma tendência crescente. Sensores de pressão menores e mais compactos estão sendo desenvolvidos, permitindo sua aplicação em uma variedade de dispositivos e sistemas. Essa miniaturização é particularmente benéfica em indústrias como a automotiva e a eletrônica, onde o espaço é limitado. Sensores menores podem ser integrados em equipamentos de forma mais eficiente, sem comprometer a precisão ou a confiabilidade.
Além disso, a inteligência artificial (IA) e o aprendizado de máquina estão começando a desempenhar um papel importante na instrumentação de pressão. Esses avanços tecnológicos permitem que os sistemas analisem grandes volumes de dados coletados pelos sensores, identificando padrões e tendências que podem não ser evidentes à primeira vista. A IA pode ajudar a otimizar processos, prever falhas e melhorar a eficiência geral dos sistemas de pressão. Por exemplo, algoritmos de aprendizado de máquina podem ser usados para ajustar automaticamente as configurações de pressão em resposta a mudanças nas condições operacionais, garantindo que os processos permaneçam dentro dos parâmetros ideais.
Outra inovação significativa é o uso de sensores de pressão baseados em tecnologia de fibra óptica. Esses sensores oferecem vantagens em termos de resistência a interferências eletromagnéticas e podem operar em ambientes extremos, onde os sensores tradicionais podem falhar. A tecnologia de fibra óptica permite medições de pressão em locais de difícil acesso e em condições adversas, como altas temperaturas e pressões extremas. Isso é especialmente útil em indústrias como a petroquímica e a exploração de petróleo e gás.
Os medidores de vazão ultrassônicos também estão se destacando como uma inovação importante na instrumentação industrial. Esses dispositivos utilizam ondas ultrassônicas para medir a vazão de líquidos e gases, oferecendo alta precisão e confiabilidade. O Medidor de vazão ultrassônico é particularmente vantajoso em aplicações onde a medição precisa é crítica, como em sistemas de controle de processos e monitoramento ambiental. A tecnologia ultrassônica é não invasiva, o que significa que não há necessidade de interromper o fluxo do fluido para realizar medições, tornando-a uma opção ideal para muitas indústrias.
Além disso, a automação industrial continua a ser uma tendência crescente na instrumentação de pressão. Sistemas automatizados permitem que as empresas integrem sensores de pressão em suas operações, melhorando a eficiência e reduzindo a necessidade de intervenção manual. A automação não apenas aumenta a precisão das medições, mas também permite que os operadores se concentrem em tarefas mais estratégicas, em vez de se preocuparem com medições manuais e ajustes constantes.
Por fim, a sustentabilidade está se tornando uma consideração cada vez mais importante na instrumentação industrial. As empresas estão buscando maneiras de reduzir seu impacto ambiental e melhorar a eficiência energética. Sensores de pressão que ajudam a monitorar e otimizar o uso de recursos, como água e energia, são essenciais para alcançar esses objetivos. A instrumentação de pressão pode desempenhar um papel crucial na identificação de vazamentos e na otimização de processos, contribuindo para a sustentabilidade das operações industriais.
Em resumo, as tendências e inovações em instrumentação industrial pressão estão moldando o futuro da indústria. A integração da IoT, sensores sem fio, miniaturização, inteligência artificial, tecnologia de fibra óptica e automação estão transformando a maneira como as empresas monitoram e controlam seus processos. À medida que a demanda por eficiência e precisão continua a crescer, a instrumentação de pressão se tornará cada vez mais sofisticada, desempenhando um papel vital na segurança, eficiência e sustentabilidade das operações industriais.
Em conclusão, a instrumentação industrial pressão é essencial para garantir a segurança, eficiência e qualidade nos processos industriais. A compreensão dos diferentes tipos de sensores de pressão e suas aplicações, juntamente com a implementação de práticas adequadas de manutenção e calibração, é fundamental para maximizar o desempenho dos sistemas. Além disso, as tendências e inovações, como a integração da IoT, a automação e o uso de tecnologias avançadas, estão moldando o futuro da instrumentação de pressão, permitindo que as indústrias se tornem mais inteligentes e sustentáveis. Investir em instrumentação de pressão não apenas melhora a operação, mas também contribui para a competitividade e a conformidade regulatória das empresas no mercado atual.