Guia Completo sobre Calibração de Transmissor de Pressão Diferencial
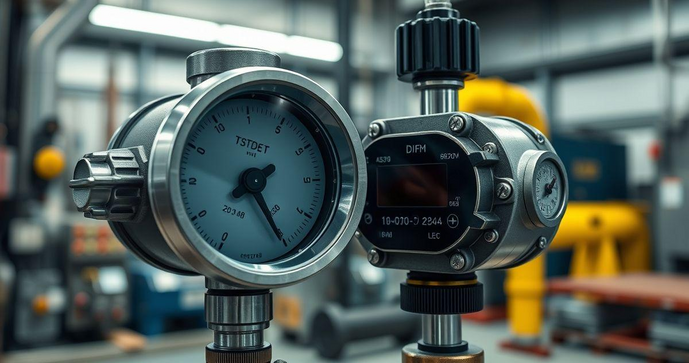
Por: Redator - 22 de Abril de 2025
Importância da Calibração em Sistemas de Medição
A calibração em sistemas de medição, especialmente para transmissores de pressão diferencial, é vital para assegurar que os dispositivos forneçam leituras precisas e confiáveis. Qualquer desvio nas medições pode resultar em falhas no controle de processos, levando a consequências perigosas, como vazamentos, explosões ou falhas operacionais.
Em ambientes industriais, a maior parte dos sistemas de controle depende de medições exatas para garantir que processos químicos, físicos e mecânicos ocorram de maneira eficiente. A diferença entre uma medição precisa e uma imprecisa pode impactar não apenas o desempenho produtivo, mas também a segurança dos trabalhadores e a proteção ao meio ambiente.
Além disso, a calibração regular é uma exigência de várias normas e regulamentações da indústria. Manter os transmissores calibrados de acordo com esses padrões ajuda as empresas a se manterem em conformidade e evita possíveis penalidades. A calibração também permite a rastreabilidade das medições, que é um requisito essencial para auditorias e certificações.
Outro aspecto importante é a economia. Medições imprecisas podem resultar em desperdício de materiais, energia e tempo, além de aumentar os custos operacionais. Ao garantir que os transmissores de pressão diferencial estejam calibrados corretamente, as empresas podem otimizar seus processos e melhorar a eficiência geral.
Em resumo, a calibração é uma prática indispensável em sistemas de medição, especialmente para transmissores de pressão diferencial. Ela promove a precisão, segurança e eficiência, sendo um investimento que proporciona retorno significativo em termos de custo e operação.
Principais Componentes do Transmissor de Pressão Diferencial
Os transmissores de pressão diferencial são dispositivos sofisticados que medem a diferença de pressão entre dois pontos. Para compreender seu funcionamento, é fundamental conhecer seus principais componentes, que incluem sensor, diafragma, sistema de referência e eletrônica de medição.
Um dos componentes principais é o sensor de pressão diferencial, que é responsável por detectar a diferença entre as pressões nos dois lados do transmissor. Este sensor pode utilizar variáveis físicas como força ou capacitância para converter a diferença de pressão em um sinal elétrico correspondente.
O diafragma, frequentemente feito de materiais flexíveis, é a parte do transmissor que separa os dois ambientes de pressão. Quando a pressão é aplicada, o diafragma se deforma, permitindo que o sensor de pressão calcule a diferença resultante. A escolha do material do diafragma é crucial, pois ele deve ser resistente e adequado para as condições do ambiente onde será utilizado.
O sistema de referência é outra parte fundamental, que estabelece um ponto fixo para a medição. Ele pode ser conectado à atmosfera ou a um reservatório calibrado de pressão. A configuração correta do sistema de referência é essencial para a precisão da medição.
Por fim, a eletrônica de medição converte o sinal gerado pelo sensor em uma forma utilizável, geralmente em um sinal elétrico como 4-20 mA ou digital. Essa eletrônica também pode incluir recursos de compensação e filtragem para melhorar a precisão e a estabilidade das leituras.
Entender estes componentes e como eles interagem é essencial para o correto funcionamento e a calibração do transmissor de pressão diferencial, garantindo medições precisas e confiáveis.
Procedimentos para Calibração de Transmissor de Pressão
Os procedimentos para calibração de um transmissor de pressão diferencial são fundamentais para garantir a precisão das medições. Este processo deve ser realizado em um ambiente controlado e com equipamentos adequados. A seguir, descrevemos um guia passo a passo para a calibração.
Primeiramente, prepare o equipamento de calibração. Isso inclui um manômetro de referência, que deve ser calibrado e rastreável a padrões reconhecidos. Certifique-se de que o manômetro e o transmissor que precisam ser calibrados estejam desconectados do sistema de processo.
Em seguida, conecte o manômetro de referência ao transmissor. As conexões devem ser feitas de forma a evitar vazamentos. Verifique se os orifícios estão devidamente vedados e se não há contaminação nos pontos de conexão.
Após a conectividade, inicie a aplicação de pressão de referência. Aplique pressão no ponto mais baixo do intervalo do transmissor, geralmente 0 psi (ou 0 bar), e ajuste o sinal de saída do transmissor utilizando o manômetro como referência. Esse passo é crucial para garantir uma leitura precisa.
Depois, aumente a pressão gradativamente para os pontos intermediários do intervalo de calibração. Para cada ponto de pressão, anote as leituras do transmissor e do manômetro. Isso ajuda a identificar qualquer desvio e a fazer os ajustes necessários na saída do transmissor.
Por fim, documente todos os dados obtidos durante a calibração. Isso deve incluir as leituras de pressão, os ajustes realizados e a data da calibração. Mantenha um registro detalhado, pois é essencial para auditorias futuras e para verificar o histórico do equipamento.
Após concluir esses passos, desconecte o manômetro de referência e verifique se o sistema do transmissor está pronto para ser reintegrado ao processo. A calibração regular garante que o transmissor de pressão diferencial opere com precisão, contribuindo para a eficiência e segurança do sistema.
Ferramentas Necessárias para a Calibração
A calibração de transmissores de pressão diferencial requer um conjunto específico de ferramentas para garantir que o processo seja realizado com precisão e eficácia. A seguir, destacamos as principais ferramentas necessárias para a calibração.
1. Manômetro de Referência: Esta é a ferramenta mais essencial. Um manômetro de alta precisão e calibrado é utilizado para comparar as leituras oferecidas pelo transmissor de pressão. Ele deve ter certificação de rastreabilidade a padrões reconhecidos para garantir a confiabilidade das medições.
2. Fonte de Pressão Calibrada: Uma fonte de pressão, como um gerador de pressão, é necessária para fornecer pressões estáveis e controladas durante o processo de calibração. Essa fonte pode ser manual ou automática, dependendo das necessidades do processo.
3. Conectores e Tubos de Transferência: É fundamental ter uma variedade de conectores e tubos adequados para realizar conexões seguras e evitar vazamentos durante a calibração. Os materiais utilizados devem ser compatíveis com as pressões e fluidos envolvidos.
4. Chave de Fenda e Ferramentas de Montagem: Ferramentas básicas de montagem, como chaves de fenda e alicates, são úteis para realizar conexões e ajustes no transmissor durante a calibração.
5. Registro de Dados: Um computador, tablet ou caderno para anotação é importante para documentar todas as leituras e os ajustes realizados durante a calibração. Manter registros precisos é essencial para auditorias e para garantir a rastreabilidade do equipamento.
6. Calibrador Multifuncional: Em algumas situações, um calibrador eletrônico que mede diversas variáveis, incluindo pressão, pode ser utilizado. Ele permite testar a precisão do transmissor de forma abrangente, facilitando o processo de calibração.
Ao reunir essas ferramentas, a calibração do transmissor de pressão diferencial torna-se mais eficiente e menos propensa a erros, garantindo medições precisas e confiáveis.
Erros Comuns na Calibração e Como Evitá-los
Calibrar transmissores de pressão diferencial pode ser um processo delicado e, muitas vezes, alguns erros comuns podem surgir, impactando a precisão das medições. Identificar e evitar esses erros é fundamental para garantir a eficácia da calibração.
1. Conexões Incorretas: Um erro comum é não conectar corretamente o manômetro de referência e o transmissor de pressão. Isso pode resultar em vazamentos ou medições imprecisas. Sempre verifique se todas as conexões estão firmes e seguras antes de iniciar o processo de calibração.
2. Falta de Manutenção do Equipamento: Usar um manômetro de referência que não esteja calibrado ou que tenha defeitos internos pode criar discrepâncias nas medições. Certifique-se de que todos os equipamentos utilizados estejam em boas condições e calibrados regularmente.
3. Ambiente de Calibração Inadequado: A calibração deve ser realizada em um ambiente controlado, livre de vibrações, poeira e variações de temperatura. Condições ambientais inadequadas podem afetar as leituras do equipamento. Escolha um local que atenda a esses requisitos para maximizar a precisão.
4. Negligenciar os Pontos de Referência: Durante o processo, é essencial calibrar o transmissor em vários pontos de referência para garantir que ele represente com precisão todo o seu intervalo. Calibrar apenas em um ponto pode levar a erros em outras partes do intervalo do transmissor.
5. Não Documentar os Resultados: Deixar de anotar as medições obtidas e ajustes realizados durante a calibração pode dificultar a identificação de problemas futuros. Mantenha um registro detalhado de cada calibração para análises posteriores e para garantir a rastreabilidade do processo.
6. Ignorar as Recomendações do Fabricante: Cada transmissor de pressão pode ter diretrizes específicas do fabricante quanto ao processo de calibração. Ignorar essas recomendações pode causar falhas operacionais. Sempre consulte o manual do operador e siga as instruções fornecidas.
Evitar esses erros comuns ao calibrar transmissores de pressão diferencial não só incrementa a precisão das medições, mas também melhora a eficiência operacional, segurança e confiabilidade do sistema como um todo.
Manutenção e Frequência Recomendada para Calibração
Manter a calibração de transmissores de pressão diferencial é um aspecto crucial para garantir medições precisas e confiáveis ao longo do tempo. A manutenção regular e a calibração são fundamentais para a eficácia e a longevidade desses dispositivos.
A frequência recomendada para calibração pode variar de acordo com o ambiente de operação, as práticas da indústria e as especificações do fabricante. No geral, muitos especialistas sugerem que a calibração seja realizada anualmente, especialmente em ambientes industriais onde as condições podem mudar rapidamente e impactar as medições.
Entretanto, há situações em que uma calibração mais frequente pode ser necessária. Por exemplo, se o transmissor estiver exposto a intervenções frequentes, como altas vibrações, temperaturas extremas ou corrosão, é aconselhável realizar calibrações cada seis meses ou até trimestralmente.
Além da calibração programada, é importante realizar verificações regulares de manutenção. Isso inclui inspeções visuais dos dispositivos, checagem de conexões elétricas e mecânicas, além de assegurar que não haja sinais de desgaste ou corrosão.
Outro aspecto crucial é a capacidade de resposta do transmissor. Sempre que ocorrer uma alteração significativa no desempenho ou nas condições de operação — como após uma reparação ou uma substituição de partes — uma calibração deve ser feita para garantir que o dispositivo continue a funcionar corretamente.
As empresas também são incentivadas a manter um registro detalhado de todas as calibrações realizadas, que deve incluir datas, resultados obtidos, ajustes realizados e condições em que a calibração foi realizada. Esse histórico será útil tanto para auditorias quanto para a identificação de padrões de desgaste ou falhas.
Em resumo, a manutenção e a frequência recomendada de calibração dos transmissores de pressão diferencial são essenciais para assegurar a precisão e eficiência das medições. Adotar uma abordagem proativa em relação a essas práticas pode evitar falhas operacionais e contribuir para um ambiente de trabalho seguro e produtivo.
A calibração de transmissores de pressão diferencial é uma prática indispensável para garantir a precisão e a confiabilidade das medições em diversos setores.
Compreender a importância dessa calibração, os principais componentes do transmissor e os procedimentos adequados são passos essenciais para o sucesso do processo.
Além disso, conhecer as ferramentas necessárias e evitar erros comuns durante a calibração ajuda a maximizar a eficácia do sistema.
A manutenção regular e a definição de frequências apropriadas para a calibração asseguram o funcionamento ideal dos transmissores, prevenindo falhas e aumentando a eficiência operacional.
Investir tempo e recursos em práticas de calibração adequadas não apenas garante a segurança e a conformidade das operações, mas também promove a durabilidade do equipamento, resultando em economias a longo prazo.
Assim, a calibração se torna não apenas uma exigência técnica, mas também uma estratégia inteligente para otimizar processos e reduzir riscos nas operações industriais.