Calibração in loco: Garanta A Precisão em seus Equipamentos
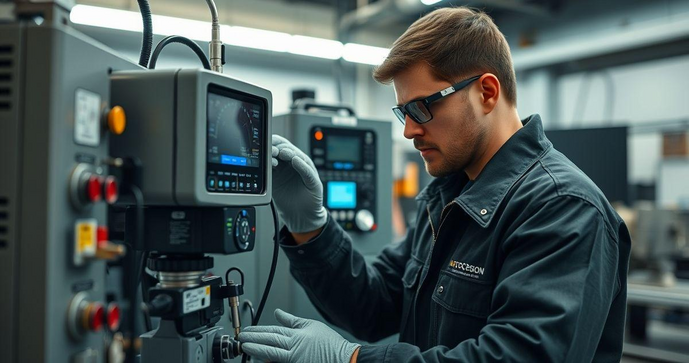
Por: Redator - 26 de Abril de 2025
Importância da Calibração In Loco para Equipamentos
A calibração in loco é fundamental para assegurar que os equipamentos operam dentro das especificações exigidas. Muitas indústrias dependem de medições precisas para garantir a qualidade dos produtos e a segurança dos processos. Ao realizar a calibração no próprio local de uso, as empresas conseguem evitar desvio de padrões, que podem resultar em perdas financeiras e desperdício de recursos.
Um aspecto chave da calibração in loco é a sua capacidade de reduzir o tempo de inatividade. Ao evitar a necessidade de transporte de equipamentos para laboratórios externos, as organizações não apenas economizam tempo, mas também mantêm a continuidade nas operações. Essa abordagem é especialmente valiosa em ambientes onde a precisão é crítica, como laboratórios, fábricas e plantas industriais.
Outra razão importante para implementar a calibração in loco é a conveniência e a personalização do processo. Os técnicos podem calibrar os instrumentos nas próprias condições de operação, assegurando que eles estejam ajustados para o ambiente específico em que serão utilizados. Esta personalização melhora a precisão e a confiabilidade das medições, otimizando o desempenho dos equipamentos ao longo do tempo.
A calibração in loco também facilita a conformidade com normas regulatórias e padrões industriais. Muitas organizações devem atender a exigências rigorosas relacionadas à calibração e verificação de seus equipamentos. Realizar esse processo no local permite uma documentação mais fácil e acessível, o que ajuda na manutenção da conformidade com exigências legais e certificações de qualidade.
Por fim, investir em calibração in loco significa priorizar a qualidade e a eficiência nas operações. Empresas que adotam essa prática frequentemente observam melhorias na qualidade do produto final, além da satisfação do cliente. Portanto, a calibração in loco não é apenas uma questão técnica, mas um componente estratégico para o sucesso a longo prazo de qualquer organização que dependa de medidas precisas.
Passo a Passo da Calibração In Loco
A calibração in loco requer um planejamento cuidadoso e a execução de etapas específicas para garantir a precisão dos equipamentos. A seguir, descrevemos um passo a passo que pode ser seguido para realizar este processo de forma eficaz.
1. Preparação do Equipamento: Antes de iniciar a calibração, é essencial que o equipamento esteja limpo e em boas condições de funcionamento. Verifique se há desgastes visíveis ou peças danificadas que possam interferir na calibração.
2. Coleta de Informações: Reúna todos os manuais e especificações técnicas dos equipamentos que serão calibrados. É importante estar familiarizado com os requisitos do fabricante para uma calibração adequada.
3. Ferramentas Necessárias: Certifique-se de ter todas as ferramentas e dispositivos de calibração disponíveis. Isso pode incluir instrumentos de referência, medidores, ferramentas de ajuste e sistemas de comunicação. Assegure-se de que essas ferramentas estejam calibradas e em boas condições antes do uso.
4. Ambientação e Condições de Trabalho: Avalie as condições do ambiente onde a calibração será realizada. Fatores como temperatura, umidade e vibração podem afetar as medições. Tente realizar a calibração em um ambiente controlado, se possível.
5. Execução da Calibração: Siga as instruções do fabricante para realizar a calibração. Isso geralmente envolve a comparação das medições do equipamento com um padrão de referência e fazer os ajustes necessários para garantir que as medições estejam dentro das especificações.
6. Documentação: Após a calibração, é crucial registrar todas as informações relevantes, incluindo as medições antes e depois da calibração, os ajustes realizados e as condições ambientais. Esses registros são importantes para auditorias e para manter a conformidade com normas regulatórias.
7. Teste e Verificação: Após a calibração, realize testes para confirmar que o equipamento opera corretamente e que as medições estão precisas. Isso pode incluir medições de verificação em duplicata para garantir que os resultados sejam consistentes.
8. Manutenção Programada: Desenvolva um cronograma de manutenção e calibração regular com base nas recomendações do fabricante e na frequência de uso do equipamento. Isso ajudará a manter a precisão e a confiabilidade a longo prazo.
Cumprindo essas etapas, a calibração in loco pode ser realizada de forma eficiente, assegurando a precisão e a confiabilidade dos equipamentos utilizados na sua operação.
Ferramentas Necessárias para Calibração In Loco
Para a realização da calibração in loco, é fundamental ter à disposição um conjunto de ferramentas específicas que garantam a precisão e a eficiência do processo. Abaixo, listamos as principais ferramentas necessárias para a calibração de equipamentos.
1. Instrumentos de Referência: Estes são dispositivos altamente precisos utilizados como padrão de comparação durante a calibração. Eles devem ser periodicamente calibrados para garantir que suas medições sejam confiáveis e exatas.
2. Medidores de Precisão: Equipamentos como multímetros, calibradores de pressão e termômetros devem ser utilizados para medir os parâmetros exatos que estão sendo verificados. A escolha do medidor deve ser adequada ao tipo de equipamento a ser calibrado.
3. Ferramentas de Ajuste: Garantir que o equipamento seja ajustado corretamente pode exigir ferramentas como chaves de fenda, alicates e chaves ajustáveis. Essas ferramentas são essenciais para realizar ajustes físicos e mecânicos necessários durante a calibração.
4. Software de Calibração: Em muitos casos, softwares especializados são utilizados para registrar medições e resultados de calibração. Eles podem ajudar a automatizar o processo e garantir que todos os dados sejam documentados corretamente.
5. Equipamentos de Comunicação: Em calibrações que envolvem sistemas eletrônicos, pode ser necessário o uso de cabos de comunicação, adaptadores e interfaces para conectar os equipamentos de teste aos sistemas que estão sendo calibrados.
6. Equipamentos de Proteção Individual (EPIs): Ao realizar a calibração, é fundamental garantir a segurança do técnico. A utilização de EPIs, como luvas, óculos de proteção e aventais, é recomendada para prevenir acidentes e garantir um ambiente de trabalho seguro.
7. Documentação e Manuais: Ter acesso a manuais do usuário e procedimentos de calibração específicos é crucial. Essa documentação oferece orientações detalhadas sobre como calibrar cada equipamento de maneira adequada.
Com as ferramentas adequadas, a calibração in loco pode ser realizada de maneira eficaz, garantindo que os equipamentos estejam sempre operando com precisão e dentro das especificações necessárias. Planejar e organizar essas ferramentas antes da calibração será essencial para o sucesso do processo.
Benefícios da Calibração In Loco no Ambiente de Trabalho
A calibração in loco oferece uma série de benefícios significativos para o ambiente de trabalho, contribuindo para a eficiência operacional e a qualidade dos produtos e serviços.
A seguir, destacamos alguns dos principais benefícios dessa prática.
1. Redução do Tempo de Inatividade: Um dos maiores benefícios da calibração in loco é a diminuição do tempo em que os equipamentos ficam fora de operação. Ao realizar a calibração no local, evita-se o transporte de instrumentos para laboratórios externos, permitindo que os processos continuem funcionando com mínima interrupção.
2. Precisão Aumentada: Calibrar os equipamentos nas condições específicas de operação garante medições mais precisas e confiáveis. Essa abordagem considera fatores como temperatura, umidade e outros parâmetros ambientais que podem impactar a performance dos equipamentos.
3. Conformidade com Normas: Muitas indústrias estão sujeitas a regulamentações rigorosas que exigem calibrações frequentes. A calibração in loco facilita a conformidade com essas normas, garantindo que os equipamentos atendam aos requisitos legais e evitando possíveis penalidades.
4. Melhoria da Qualidade do Produto: A certeza de que os equipamentos estão calibrados e operando com precisão impacta diretamente a qualidade dos produtos finais. Com medições exatas, minimiza-se o risco de produtos defeituosos, garantindo maior satisfação do cliente.
5. Facilidade de Registro e Documentação: A calibração in loco permite que todos os registros necessários sejam feitos no local, facilitando a documentação de calibrações e a manutenção de relatórios atualizados. Isso simplifica processos de auditoria e acompanhamento de equipamientos.
6. Economia de Custos: Embora possa haver um custo inicial associado à implementação de calibração in loco, a longo prazo, essa prática ajuda a reduzir custos operacionais ao evitar despesas relacionadas a paradas de produção e retrabalho devido a equipamentos mal calibrados.
7. Flexibilidade e Adaptabilidade: A calibração in loco oferece maior flexibilidade para responder rapidamente às necessidades operacionais. Quando novos equipamentos são introduzidos ou as especificações mudam, é mais fácil fazer ajustes no local, sem a necessidade de retornos repetidos a um laboratório.
Em resumo, a implementação da calibração in loco no ambiente de trabalho não apenas agiliza as operações, mas também contribui para a eficiência, qualidade e segurança. Essa abordagem é um investimento inteligente para empresas que buscam excelência em seus processos.
Diferenças entre Calibração In Loco e Externa
A calibração de equipamentos pode ser realizada de duas maneiras principais: in loco e externa. Cada uma delas possui características específicas que podem influenciar a decisão sobre qual método utilizar no ambiente de trabalho. A seguir, apresentamos as principais diferenças entre a calibração in loco e a calibração externa.
1. Localização da Calibração: A calibração in loco é realizada no próprio local onde o equipamento está instalado e sendo utilizado, enquanto a calibração externa acontece em laboratórios ou instalações específicas de calibração, onde os equipamentos são transportados para serem calibrados.
2. Tempo de Execução: A calibração in loco tende a ser mais rápida, pois elimina o tempo de transporte dos equipamentos. Por outro lado, a calibração externa pode levar mais tempo, uma vez que envolve logística de deslocamento e o processo de calibração propriamente dito no laboratório.
3. Precisão em Condições Reais: A calibração in loco permite ajustes que consideram as condições reais de operação, como temperatura e umidade, resultando em medições mais precisas para o ambiente específico de uso. Já na calibração externa, as condições no laboratório podem ser diferentes, podendo não refletir com precisão o funcionamento do equipamento no local de uso.
4. Documentação e Regulamentação: A calibração externa muitas vezes fornece um relatório de calibração com maior detalhamento técnico e rastreabilidade ao longo do tempo, enquanto a calibração in loco pode ter documentação mais simples, adaptada às necessidades imediatas da operação.
5. Custo: Geralmente, a calibração in loco é mais econômica a longo prazo, pois reduz custos com transporte e tempo de inatividade. Em contrapartida, a calibração externa pode ter custos adicionais associados ao deslocamento dos equipamentos e à taxa de serviço do laboratório.
6. Flexibilidade: A calibração in loco oferece maior flexibilidade e pode ser programada com maior facilidade para se ajustar às necessidades operacionais. A calibração externa pode exigir agendamento e pode ser limitada pela disponibilidade do laboratório.
7. Necessidade de Especialização: Algumas calibrações externas podem contar com uma equipe altamente especializada com acesso a equipamentos de calibração de última geração, enquanto a calibração in loco depende da competência e da qualificação dos técnicos presentes no local.
Em resumo, tanto a calibração in loco quanto a externa têm suas vantagens e desvantagens. A escolha entre ambos os métodos deve considerar fatores como precisão necessária, custo, tempo disponível e características do equipamento a ser calibrado. Escolher a abordagem correta pode garantir que os processos operacionais funcionem de maneira suave e eficiente.
Erros Comuns na Calibração In Loco e Como Evitá-los
A calibração in loco é uma prática essencial para garantir a precisão dos equipamentos, mas pode estar sujeita a erros que comprometem a qualidade do processo. Conhecer esses erros comuns e como evitá-los é fundamental para garantir uma calibração eficaz. A seguir, apresentamos alguns dos erros mais frequentes e as estratégias para preveni-los.
1. Falta de Preparação do Equipamento: Um erro comum é não realizar uma verificação prévia do equipamento antes da calibração. Para evitar isso, deve-se sempre fazer uma limpeza e inspeção do equipamento para assegurar que está em boas condições. Reparos necessários devem ser feitos antes da calibração.
2. Ignorar as Condições Ambientais: As condições de temperatura e umidade podem impactar a calibração. Para prevenir esse erro, é essencial realizar a calibração em um ambiente controlado sempre que possível e documentar as condições ambientais durante o processo para garantir a precisão.
3. Uso de Instrumentos de Referência Não Calibrados: Utilizar instrumentos de referência que não estão calibrados pode levar a resultados imprecisos. Sempre verifique se os instrumentos de referência estão devidamente calibrados e mantenha registros atualizados das calibrações realizadas.
4. Documentação Inadequada: Falhas na documentação podem resultar em perda de informações valiosas ou na impossibilidade de realizar auditorias. Para evitar esse problema, deve-se garantir que todos os passos da calibração sejam registrados de forma meticulosa, incluindo medições antes e depois, ajustes realizados e observações relevantes.
5. Não Realizar Testes de Verificação: Após a calibração, não testar o equipamento pode resultar em operação inadequada. É crucial realizar medições de verificação para confirmar que o equipamento opera de acordo com as especificações desejadas.
6. Pressão para Completar o Processo Rápido: A pressa em concluir o processo de calibração pode levar a erros. Para evitar isso, é importante planejar adequadamente o tempo necessário para realizar a calibração de forma rigorosa, evitando interrupções desnecessárias e priorizando a precisão.
7. Falta de Treinamento Adequado: Técnicos sem a devida qualificação podem cometer erros. Garantir que todos os envolvidos no processo de calibração recebam treinamento adequado e estejam atualizados sobre as melhores práticas é fundamental para evitar falhas.
Em conclusão, evitar erros comuns na calibração in loco requer atenção a detalhes, preparação cuidadosa e disposição para seguir procedimentos rigorosos. Implementando as práticas acima, é possível garantir que a calibração seja realizada com precisão e eficiência, resultando na confiabilidade dos equipamentos utilizados.
A calibração in loco é uma prática essencial para garantir o desempenho e a precisão dos equipamentos em diversos ambientes de trabalho.
Através da realização deste processo no local de uso, é possível reduzir o tempo de inatividade, melhorar a qualidade do produto e assegurar a conformidade regulatória.
Com a adoção de um planejamento cuidadoso, a utilização das ferramentas corretas e a mitigação de erros comuns, as organizações podem maximizar os benefícios da calibração in loco.
Dessa forma, investindo na calibração regular e na formação adequada dos profissionais envolvidos, as empresas não apenas melhoram a eficiência operacional, mas também garantem a confiabilidade de suas operações a longo prazo.