Calibração e Aferição de Instrumentos: Como Garantir Precisão e Confiabilidade em Seus Equipamentos
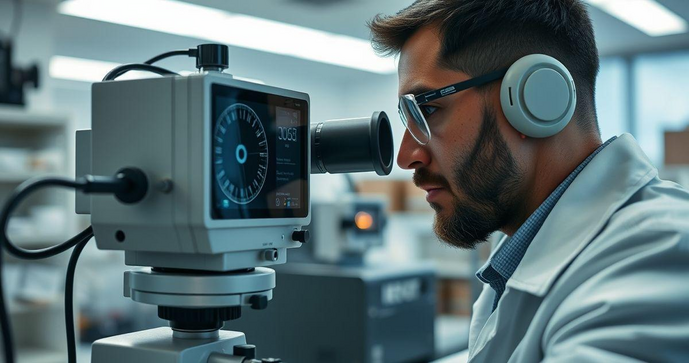
Por: Redator - 27 de Março de 2025
A calibração e aferição de instrumentos são processos fundamentais para garantir a precisão e a confiabilidade em medições em diversos setores. Esses procedimentos asseguram que os equipamentos estejam funcionando corretamente, evitando erros que podem comprometer a qualidade dos produtos e serviços. Neste artigo, abordaremos a importância da calibração e aferição, os métodos utilizados, a frequência recomendada e os erros comuns que devem ser evitados.
Importância da Calibração e Aferição de Instrumentos na Indústria
A calibração e aferição de instrumentos são processos cruciais na indústria, pois garantem que os equipamentos de medição estejam funcionando de maneira precisa e confiável. Esses procedimentos são essenciais para manter a qualidade dos produtos, a segurança dos processos e a conformidade com normas e regulamentos. Neste contexto, a calibração refere-se ao ajuste de um instrumento para que suas medições correspondam a padrões conhecidos, enquanto a aferição é o processo de verificação da precisão do instrumento em relação a esses padrões.
Um dos principais motivos pelos quais a calibração e aferição são tão importantes é a necessidade de garantir a qualidade do produto final. Em setores como farmacêutico, alimentício e químico, a precisão nas medições é vital. Por exemplo, em uma fábrica de medicamentos, a dosagem correta dos ingredientes ativos é fundamental para a eficácia do produto. Se os instrumentos de medição não estiverem calibrados corretamente, isso pode resultar em produtos fora dos padrões de qualidade, colocando em risco a saúde dos consumidores e a reputação da empresa.
Além disso, a calibração e aferição de instrumentos ajudam a evitar desperdícios e retrabalhos. Quando os instrumentos não estão funcionando corretamente, pode haver a necessidade de descartar lotes inteiros de produtos que não atendem aos padrões de qualidade. Isso não apenas gera perdas financeiras, mas também impacta a eficiência operacional da empresa. Ao garantir que os instrumentos estejam calibrados e aferidos, as indústrias podem minimizar esses riscos e otimizar seus processos produtivos.
A segurança também é um aspecto crítico que justifica a importância da calibração e aferição. Em indústrias que lidam com substâncias perigosas ou processos de alta pressão, a precisão nas medições é vital para evitar acidentes. Por exemplo, em uma planta petroquímica, a medição correta da pressão e temperatura é essencial para garantir que os processos ocorram dentro dos limites seguros. Instrumentos não calibrados podem levar a falhas catastróficas, colocando em risco a vida dos trabalhadores e causando danos ao meio ambiente.
Outro ponto a ser considerado é a conformidade com normas e regulamentos. Muitas indústrias são obrigadas a seguir padrões específicos estabelecidos por órgãos reguladores. A calibração e aferição de instrumentos são frequentemente exigidas para garantir que os processos e produtos atendam a esses requisitos. O não cumprimento pode resultar em penalidades, multas e até mesmo a suspensão das operações. Portanto, manter um programa de calibração e aferição eficaz é fundamental para garantir a conformidade e evitar problemas legais.
Além disso, a calibração e aferição de instrumentos contribuem para a melhoria contínua dos processos industriais. Ao monitorar e ajustar regularmente os instrumentos, as empresas podem identificar tendências e variações que podem indicar problemas nos processos. Isso permite que as indústrias adotem medidas corretivas antes que os problemas se tornem significativos, promovendo uma cultura de melhoria contínua e eficiência.
É importante ressaltar que a calibração e aferição não são tarefas únicas, mas sim processos contínuos. A frequência com que esses procedimentos devem ser realizados depende de vários fatores, incluindo o tipo de instrumento, a aplicação e as condições de operação. Por isso, é essencial que as indústrias desenvolvam um plano de calibração e aferição que atenda às suas necessidades específicas.
Por fim, a calibração e aferição de instrumentos são fundamentais para a Instrumentação industrial, pois garantem a precisão, a segurança e a qualidade dos processos e produtos. Investir em um programa robusto de calibração e aferição não apenas protege a saúde e a segurança dos trabalhadores, mas também contribui para a eficiência operacional e a competitividade no mercado. Portanto, as indústrias devem priorizar esses processos como parte de sua estratégia de gestão da qualidade.
Em resumo, a calibração e aferição de instrumentos são essenciais para garantir a qualidade, segurança e conformidade nas operações industriais. Ao implementar práticas eficazes de calibração e aferição, as empresas podem não apenas atender aos requisitos regulatórios, mas também melhorar sua eficiência e competitividade no mercado. A precisão nas medições é um pilar fundamental para o sucesso de qualquer operação industrial, e a calibração e aferição desempenham um papel vital nesse contexto.
Métodos Comuns de Calibração e Aferição
A calibração e aferição de instrumentos são processos essenciais para garantir a precisão e a confiabilidade das medições em diversos setores industriais. Existem vários métodos utilizados para realizar esses procedimentos, cada um com suas características e aplicações específicas. Neste artigo, abordaremos alguns dos métodos mais comuns de calibração e aferição, destacando suas vantagens e desvantagens.
Um dos métodos mais tradicionais de calibração é a calibração por comparação. Neste método, o instrumento a ser calibrado é comparado a um padrão de referência conhecido, que possui uma precisão superior. O processo envolve a medição de uma grandeza específica, como pressão, temperatura ou vazão, utilizando tanto o instrumento em teste quanto o padrão de referência. As medições são então comparadas, e ajustes são feitos no instrumento, se necessário. Este método é amplamente utilizado devido à sua simplicidade e eficácia, mas requer que o padrão de referência seja mantido em condições controladas para garantir a precisão.
Outro método comum é a calibração por ajuste. Neste caso, o instrumento é ajustado diretamente para que suas medições correspondam aos valores do padrão de referência. Esse método é frequentemente utilizado em instrumentos que possuem um mecanismo de ajuste interno, como termômetros e manômetros. A calibração por ajuste é vantajosa porque permite que o instrumento seja ajustado para fornecer medições precisas, mas pode ser mais complexa, pois requer conhecimento técnico para realizar os ajustes adequados.
A calibração em campo é um método que se tornou cada vez mais popular, especialmente em indústrias que utilizam instrumentos móveis ou que operam em locais remotos. Neste método, os instrumentos são calibrados no local de uso, utilizando padrões de referência portáteis. A calibração em campo é conveniente, pois elimina a necessidade de transportar os instrumentos para um laboratório, mas pode apresentar desafios em termos de controle ambiental e condições de operação. É importante garantir que as condições de temperatura e pressão sejam monitoradas durante o processo de calibração para evitar resultados imprecisos.
Além disso, a calibração por simulação é um método que utiliza equipamentos de teste que simulam as condições de operação do instrumento. Esse método é particularmente útil para instrumentos que não podem ser ajustados diretamente ou que não possuem um padrão de referência disponível. A calibração por simulação permite que os operadores verifiquem o desempenho do instrumento em condições específicas, garantindo que ele funcione corretamente em situações reais. No entanto, esse método pode ser mais complexo e exigir equipamentos especializados.
A aferição de instrumentos também pode ser realizada por meio de métodos de verificação. Neste caso, o instrumento é testado em relação a um padrão de referência, mas não é ajustado. A verificação é útil para determinar se o instrumento está dentro das especificações aceitáveis, sem a necessidade de realizar ajustes. Esse método é frequentemente utilizado em situações em que a calibração não é prática ou necessária, como em instrumentos que são usados apenas ocasionalmente.
Outro método importante é a Calibração RBC, que é amplamente utilizada para instrumentos de medição de vazão, como fluxômetros. Este método envolve a comparação das medições do instrumento com um padrão de referência em condições controladas. A Calibração RBC é especialmente eficaz para garantir a precisão em medições de vazão, que são críticas em muitos processos industriais. A utilização de padrões de referência confiáveis e a realização de testes em condições controladas são fundamentais para o sucesso deste método.
Além dos métodos mencionados, a calibração e aferição também podem ser realizadas utilizando software especializado. Esses sistemas permitem que os operadores realizem medições e calibrações de forma automatizada, aumentando a eficiência e reduzindo a possibilidade de erros humanos. O uso de software para calibração é especialmente útil em ambientes industriais onde a precisão e a rastreabilidade são essenciais.
É importante ressaltar que a escolha do método de calibração e aferição deve levar em consideração diversos fatores, como o tipo de instrumento, a aplicação, as condições de operação e os recursos disponíveis. Cada método possui suas vantagens e desvantagens, e a seleção do mais adequado pode impactar diretamente a precisão e a confiabilidade das medições.
Em resumo, os métodos comuns de calibração e aferição incluem calibração por comparação, calibração por ajuste, calibração em campo, calibração por simulação, verificação e calibração RBC. Cada um desses métodos desempenha um papel importante na garantia da precisão e confiabilidade dos instrumentos de medição. Ao entender as características e aplicações de cada método, as indústrias podem implementar práticas eficazes de calibração e aferição, assegurando a qualidade e a segurança de seus processos.
Frequência Recomendada para Calibração e Aferição de Instrumentos
A calibração e aferição de instrumentos são processos essenciais para garantir a precisão e a confiabilidade das medições em diversos setores industriais. No entanto, a eficácia desses processos depende não apenas da qualidade dos métodos utilizados, mas também da frequência com que são realizados. A determinação da frequência adequada para calibração e aferição é crucial para manter a integridade dos instrumentos e, consequentemente, a qualidade dos produtos e serviços oferecidos. Neste artigo, discutiremos os fatores que influenciam a frequência recomendada para calibração e aferição de instrumentos.
Um dos principais fatores a considerar ao estabelecer a frequência de calibração é o tipo de instrumento. Diferentes instrumentos têm diferentes níveis de sensibilidade e precisão, o que pode afetar a necessidade de calibração. Por exemplo, instrumentos de medição de alta precisão, como balanças analíticas e manômetros, podem exigir calibrações mais frequentes do que instrumentos menos sensíveis. Em geral, instrumentos que operam em condições extremas ou que são utilizados em aplicações críticas devem ser calibrados com mais frequência.
Outro fator importante é a frequência de uso do instrumento. Instrumentos que são utilizados diariamente ou em operações contínuas estão mais sujeitos a desgastes e variações de desempenho. Portanto, é recomendável que esses instrumentos sejam calibrados com maior regularidade. Por outro lado, instrumentos que são utilizados esporadicamente podem ter uma frequência de calibração menos intensa. É fundamental que as indústrias avaliem o uso de cada instrumento e ajustem a frequência de calibração de acordo.
As condições ambientais também desempenham um papel significativo na determinação da frequência de calibração. Instrumentos que operam em ambientes com variações extremas de temperatura, umidade ou pressão podem sofrer alterações em seu desempenho. Por exemplo, em indústrias químicas, onde os instrumentos podem ser expostos a substâncias corrosivas, a calibração deve ser realizada com mais frequência para garantir que os instrumentos permaneçam precisos e confiáveis. Portanto, é essencial considerar as condições de operação ao estabelecer um cronograma de calibração.
Além disso, a conformidade com normas e regulamentos pode influenciar a frequência de calibração. Muitas indústrias são obrigadas a seguir padrões específicos estabelecidos por órgãos reguladores, que podem incluir requisitos de calibração. Por exemplo, na indústria farmacêutica, a calibração de instrumentos é frequentemente exigida para garantir a conformidade com as boas práticas de fabricação. As empresas devem estar cientes das regulamentações aplicáveis e garantir que seus instrumentos sejam calibrados de acordo com as diretrizes estabelecidas.
Outro aspecto a ser considerado é a história de desempenho do instrumento. Se um instrumento apresentar problemas frequentes ou inconsistências nas medições, pode ser necessário aumentar a frequência de calibração. A análise de dados históricos de desempenho pode ajudar as indústrias a identificar padrões e determinar se ajustes na frequência de calibração são necessários. Além disso, a realização de auditorias regulares pode fornecer informações valiosas sobre a eficácia do programa de calibração e ajudar a identificar áreas que precisam de atenção.
As indústrias também podem se beneficiar da implementação de um programa de gerenciamento de calibração. Esse programa deve incluir um cronograma de calibração, registros de calibração e procedimentos para a realização de calibrações. Um Laboratório de Calibração pode ser um recurso valioso para ajudar as empresas a estabelecer e manter um programa eficaz de calibração. Esses laboratórios oferecem serviços de calibração e podem fornecer orientações sobre a frequência recomendada com base nas necessidades específicas de cada instrumento e aplicação.
Em resumo, a frequência recomendada para calibração e aferição de instrumentos depende de vários fatores, incluindo o tipo de instrumento, a frequência de uso, as condições ambientais, a conformidade com normas e regulamentos e a história de desempenho do instrumento. As indústrias devem avaliar cuidadosamente esses fatores e implementar um cronograma de calibração que atenda às suas necessidades específicas. A calibração regular não apenas garante a precisão e a confiabilidade das medições, mas também contribui para a qualidade dos produtos e serviços oferecidos, aumentando a competitividade no mercado.
Por fim, é importante ressaltar que a calibração e aferição de instrumentos não são tarefas únicas, mas sim processos contínuos que exigem atenção e comprometimento. Ao estabelecer uma frequência adequada para calibração e aferição, as indústrias podem garantir que seus instrumentos permaneçam precisos e confiáveis, promovendo a eficiência operacional e a satisfação do cliente.
Erros Comuns na Calibração e Como Evitá-los
A calibração de instrumentos é um processo crítico para garantir a precisão e a confiabilidade das medições em diversos setores industriais. No entanto, erros podem ocorrer durante esse processo, comprometendo a eficácia da calibração e, consequentemente, a qualidade dos produtos e serviços. Neste artigo, abordaremos alguns dos erros mais comuns na calibração e como evitá-los, garantindo que os instrumentos funcionem de maneira adequada e eficiente.
Um dos erros mais frequentes na calibração é a falta de um padrão de referência adequado. A calibração deve ser realizada em comparação com um padrão de referência que possua uma precisão superior ao instrumento em teste. Se o padrão de referência não for confiável ou não estiver calibrado corretamente, as medições do instrumento também estarão comprometidas. Para evitar esse erro, é fundamental utilizar padrões de referência que sejam rastreáveis a laboratórios acreditados e que estejam dentro do intervalo de calibração do instrumento.
Outro erro comum é a calibração em condições inadequadas. A temperatura, umidade e pressão podem afetar significativamente o desempenho dos instrumentos. Realizar a calibração em ambientes que não atendem às especificações recomendadas pode resultar em medições imprecisas. Para evitar esse problema, é importante garantir que a calibração seja realizada em condições controladas, conforme as diretrizes do fabricante. Além disso, é essencial monitorar as condições ambientais durante o processo de calibração para garantir que permaneçam dentro dos limites aceitáveis.
A falta de treinamento adequado dos operadores também é um fator que contribui para erros na calibração. Operadores não treinados podem não entender completamente os procedimentos de calibração, o que pode levar a erros na execução. Para evitar esse problema, as empresas devem investir em treinamento contínuo para seus funcionários, garantindo que eles estejam atualizados sobre as melhores práticas de calibração e as especificações dos instrumentos. Um operador bem treinado é fundamental para a realização de calibrações precisas e confiáveis.
Além disso, a falta de documentação adequada pode resultar em erros na calibração. Registros incompletos ou ausentes podem dificultar a rastreabilidade das calibrações e a identificação de problemas. É essencial manter registros detalhados de todas as calibrações realizadas, incluindo datas, resultados, padrões utilizados e quaisquer ajustes feitos. Essa documentação não apenas ajuda a garantir a conformidade com as normas, mas também permite que as empresas identifiquem tendências e problemas recorrentes que possam exigir atenção.
Outro erro comum é a calibração de instrumentos que não estão em condições adequadas de funcionamento. Antes de realizar a calibração, é importante verificar se o instrumento está limpo e livre de danos. Instrumentos sujos ou danificados podem apresentar medições imprecisas, mesmo após a calibração. Para evitar esse problema, as empresas devem implementar procedimentos de manutenção preventiva que incluam a limpeza e inspeção regular dos instrumentos antes da calibração.
A calibração de instrumentos em intervalos inadequados também é um erro que pode comprometer a precisão das medições. A frequência de calibração deve ser determinada com base em vários fatores, como o tipo de instrumento, a frequência de uso e as condições ambientais. Calibrar um instrumento com muita frequência pode resultar em custos desnecessários, enquanto calibrações insuficientes podem levar a medições imprecisas. As empresas devem desenvolver um cronograma de calibração que leve em consideração esses fatores e que seja revisado regularmente para garantir sua eficácia.
Outro aspecto a ser considerado é a utilização de equipamentos de calibração inadequados. O uso de equipamentos que não são apropriados para o tipo de instrumento em teste pode resultar em medições imprecisas. Por exemplo, ao calibrar um Medidor de vazão ultrassônico, é fundamental utilizar equipamentos de calibração que sejam compatíveis e que atendam às especificações do fabricante. As empresas devem garantir que todos os equipamentos de calibração estejam em boas condições de funcionamento e que sejam adequados para os instrumentos que estão sendo calibrados.
Por fim, a falta de revisão e auditoria dos processos de calibração pode levar a erros não detectados. As empresas devem implementar um sistema de auditoria regular para revisar os procedimentos de calibração e identificar áreas que precisam de melhorias. Isso pode incluir a análise de registros de calibração, a verificação de padrões de referência e a avaliação do desempenho dos operadores. A auditoria regular ajuda a garantir que os processos de calibração estejam sendo seguidos corretamente e que quaisquer problemas sejam identificados e corrigidos rapidamente.
Em resumo, os erros comuns na calibração incluem a falta de um padrão de referência adequado, calibração em condições inadequadas, falta de treinamento dos operadores, documentação insuficiente, calibração de instrumentos em condições inadequadas, calibração em intervalos inadequados, uso de equipamentos inadequados e falta de revisão dos processos. Ao estar ciente desses erros e implementar medidas para evitá-los, as empresas podem garantir que seus instrumentos sejam calibrados de maneira precisa e confiável, promovendo a qualidade e a segurança em suas operações.
Em conclusão, a calibração e aferição de instrumentos são essenciais para a manutenção da qualidade e segurança em processos industriais. Através da compreensão da importância desses procedimentos, dos métodos adequados, da frequência recomendada e da identificação de erros comuns, as empresas podem implementar práticas eficazes que garantam a precisão das medições. Investir em calibração e aferição não apenas protege a integridade dos produtos, mas também fortalece a confiança dos clientes e a reputação da empresa no mercado. Portanto, é fundamental que as indústrias adotem uma abordagem proativa em relação à calibração e aferição, assegurando que seus instrumentos estejam sempre em conformidade e funcionando de maneira ideal.