Calibração de Instrumentos de Pressão: Como Garantir Precisão e Confiabilidade em Seus Equipamentos
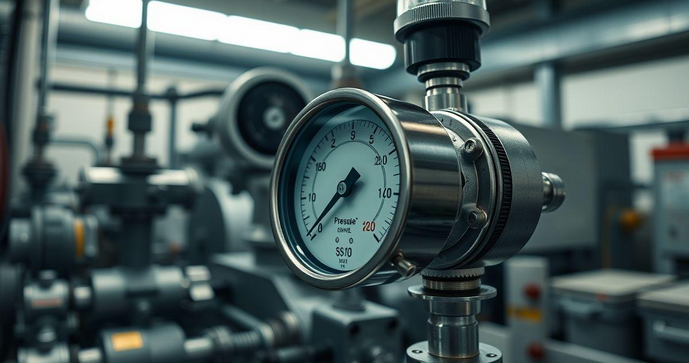
Por: Redator - 25 de Março de 2025
A calibração de instrumentos de pressão é um processo fundamental para garantir a precisão e a confiabilidade das medições em diversos setores, como industrial e laboratorial. Com a crescente demanda por qualidade e segurança, entender a importância da calibração e os métodos disponíveis se torna essencial. Neste artigo, abordaremos os principais aspectos da calibração de instrumentos de pressão, incluindo sua importância, métodos comuns, frequência recomendada e erros a serem evitados.
Importância da Calibração de Instrumentos de Pressão na Indústria
A calibração de instrumentos de pressão é um aspecto crucial na indústria, pois garante que os equipamentos estejam funcionando de maneira precisa e confiável. A precisão nas medições de pressão é vital para a segurança, eficiência e qualidade dos processos industriais. Quando os instrumentos de pressão não estão calibrados corretamente, podem ocorrer erros que impactam diretamente a produção e a segurança dos trabalhadores.
Um dos principais motivos para a calibração de instrumentos de pressão é a necessidade de conformidade com normas e regulamentos. Muitas indústrias operam sob rigorosos padrões de qualidade e segurança, que exigem a calibração regular de equipamentos. Isso é especialmente verdadeiro em setores como farmacêutico, petroquímico e alimentício, onde a precisão das medições é fundamental para garantir a qualidade do produto final. A calibração ajuda a evitar não conformidades que podem resultar em multas, interrupções na produção e até mesmo ações legais.
Além da conformidade regulatória, a calibração de instrumentos de pressão é essencial para a segurança operacional. Instrumentos imprecisos podem levar a leituras erradas, resultando em pressões excessivas ou insuficientes em sistemas críticos. Isso pode causar falhas catastróficas, como explosões, vazamentos ou falhas de equipamentos. Por exemplo, em uma planta petroquímica, uma leitura incorreta de pressão pode resultar em uma explosão, colocando em risco a vida dos trabalhadores e causando danos significativos ao ambiente. Portanto, a calibração regular é uma prática preventiva que ajuda a mitigar esses riscos.
Outro aspecto importante da calibração é a eficiência operacional. Instrumentos de pressão calibrados corretamente garantem que os processos industriais funcionem dentro dos parâmetros ideais. Isso não apenas melhora a qualidade do produto, mas também reduz o desperdício de materiais e energia. Por exemplo, em um sistema de controle de processos, uma leitura precisa de pressão permite que os operadores ajustem as condições de operação para otimizar a produção. Isso resulta em uma operação mais eficiente e econômica, aumentando a competitividade da empresa no mercado.
A calibração também desempenha um papel fundamental na manutenção preditiva. Ao monitorar regularmente a precisão dos instrumentos de pressão, as empresas podem identificar problemas antes que se tornem críticos. Isso permite que as equipes de manutenção realizem intervenções programadas, evitando paradas não planejadas e prolongando a vida útil dos equipamentos. A manutenção preditiva é uma abordagem proativa que ajuda a reduzir custos operacionais e a melhorar a confiabilidade dos sistemas.
Além disso, a calibração de instrumentos de pressão é essencial para a coleta de dados precisos. Em muitas indústrias, os dados de pressão são utilizados para análises e relatórios que influenciam decisões estratégicas. Se os instrumentos não estiverem calibrados corretamente, os dados coletados podem ser imprecisos, levando a decisões erradas. Isso pode afetar não apenas a produção, mas também a pesquisa e desenvolvimento de novos produtos. Portanto, garantir a precisão das medições é fundamental para a tomada de decisões informadas.
Outro ponto a ser considerado é a importância da calibração em sistemas de automação industrial. Com o avanço da tecnologia, muitos processos industriais estão se tornando cada vez mais automatizados. Instrumentos de pressão calibrados corretamente são essenciais para garantir que os sistemas automatizados funcionem de maneira eficaz. A automação depende de dados precisos para tomar decisões em tempo real, e qualquer erro nas medições pode comprometer a operação do sistema. Portanto, a calibração é uma parte integrante da automação industrial.
Por fim, a calibração de instrumentos de pressão não deve ser vista apenas como uma obrigação regulatória, mas como uma prática que traz benefícios significativos para a operação industrial. As empresas que investem em calibração regular não apenas garantem a conformidade, mas também melhoram a segurança, a eficiência e a qualidade de seus processos. Isso resulta em uma operação mais sustentável e competitiva no mercado.
Para mais informações sobre a calibração e a importância da instrumentação na indústria, você pode conferir o site sobre Instrumentação industrial . A compreensão e a aplicação adequadas da calibração de instrumentos de pressão são fundamentais para o sucesso de qualquer operação industrial, e as empresas devem priorizar essa prática para garantir um desempenho ideal e seguro.
Métodos Comuns de Calibração de Instrumentos de Pressão
A calibração de instrumentos de pressão é um processo essencial para garantir a precisão e a confiabilidade das medições em diversas aplicações industriais. Existem vários métodos de calibração que podem ser utilizados, dependendo do tipo de instrumento, da faixa de pressão e das condições operacionais. Neste artigo, abordaremos os métodos mais comuns de calibração de instrumentos de pressão, destacando suas características e aplicações.
Um dos métodos mais tradicionais de calibração é o método de comparação. Neste processo, o instrumento a ser calibrado é comparado a um padrão de referência conhecido, que possui uma precisão superior. O padrão de referência pode ser um manômetro de alta precisão ou um calibrador de pressão. Durante a calibração, o instrumento é submetido a uma série de pressões conhecidas, e as leituras são registradas. As diferenças entre as leituras do instrumento e as do padrão de referência são então analisadas para determinar a precisão do instrumento. Este método é amplamente utilizado devido à sua simplicidade e eficácia.
Outro método comum é a calibração por ponto fixo. Neste método, o instrumento é calibrado em pontos específicos de sua faixa de medição. Por exemplo, se um manômetro tem uma faixa de 0 a 100 psi, a calibração pode ser realizada em pontos como 0 psi, 25 psi, 50 psi, 75 psi e 100 psi. Esse método é útil para identificar desvios em pontos críticos da faixa de medição, permitindo ajustes mais precisos. A calibração por ponto fixo é frequentemente utilizada em aplicações onde a precisão em pontos específicos é mais importante do que a precisão em toda a faixa.
A calibração em linha é outro método que tem ganhado popularidade, especialmente em ambientes industriais onde a interrupção do processo deve ser minimizada. Neste método, o instrumento de pressão é calibrado enquanto está instalado no sistema. Um calibrador portátil é conectado ao sistema, e as medições são realizadas sem remover o instrumento. Isso permite que os operadores verifiquem a precisão do instrumento sem interromper a operação. A calibração em linha é particularmente útil em processos contínuos, onde a manutenção da produção é crítica.
Além disso, a calibração por simulação é um método que utiliza equipamentos de simulação para gerar pressões conhecidas. Este método é frequentemente utilizado em laboratórios de calibração, onde um simulador de pressão pode ser ajustado para fornecer pressões específicas. O instrumento a ser calibrado é conectado ao simulador, e as leituras são comparadas. A calibração por simulação é vantajosa porque permite uma calibração rápida e precisa, além de ser útil para instrumentos que não podem ser testados em condições reais de operação.
Outro método que merece destaque é a calibração por transferência. Neste processo, um instrumento de referência é utilizado para transferir a calibração para o instrumento a ser testado. O instrumento de referência é calibrado em um laboratório de calibração acreditado e, em seguida, utilizado para verificar a precisão do instrumento em campo. Este método é útil para garantir que os instrumentos de pressão estejam sempre dentro das especificações, mesmo quando não podem ser enviados para calibração em laboratório.
Além dos métodos mencionados, a calibração de instrumentos de pressão também pode ser realizada utilizando técnicas de calibração automática. Esses sistemas automatizados utilizam software e hardware para realizar a calibração de forma rápida e precisa. A calibração automática é especialmente útil em ambientes onde a precisão e a eficiência são essenciais, como em fábricas e instalações de produção em larga escala. Esses sistemas podem realizar calibrações em múltiplos instrumentos simultaneamente, economizando tempo e recursos.
É importante ressaltar que, independentemente do método escolhido, a calibração deve ser realizada por profissionais qualificados e com equipamentos adequados. A precisão da calibração depende não apenas do método, mas também da qualidade dos instrumentos de referência utilizados. Além disso, a calibração deve ser realizada em intervalos regulares, conforme recomendado pelo fabricante do instrumento e pelas normas da indústria.
Para garantir a precisão e a confiabilidade das medições, muitas empresas optam por serviços de calibração especializados. Esses serviços oferecem calibração de instrumentos de pressão, como manômetros e transdutores, utilizando métodos avançados e equipamentos de última geração. Um exemplo é a Calibração RBC , que proporciona serviços de calibração de alta qualidade, assegurando que os instrumentos estejam sempre dentro das especificações exigidas.
Em resumo, a calibração de instrumentos de pressão é um processo vital para garantir a precisão e a confiabilidade das medições em diversas aplicações industriais. Os métodos de calibração, como comparação, ponto fixo, em linha, simulação e transferência, oferecem diferentes abordagens para atender às necessidades específicas de cada aplicação. A escolha do método adequado depende de fatores como o tipo de instrumento, a faixa de pressão e as condições operacionais. A calibração regular e adequada é essencial para garantir a segurança, a eficiência e a qualidade dos processos industriais.
Frequência Recomendada para Calibração de Instrumentos de Pressão
A calibração de instrumentos de pressão é uma prática essencial para garantir a precisão e a confiabilidade das medições em diversos setores industriais. No entanto, a eficácia da calibração não depende apenas da qualidade do processo, mas também da frequência com que ela é realizada. A determinação da frequência recomendada para a calibração de instrumentos de pressão é um aspecto crítico que pode impactar diretamente a segurança, a eficiência e a qualidade dos processos. Neste artigo, discutiremos os fatores que influenciam a frequência de calibração e as diretrizes gerais a serem seguidas.
Um dos principais fatores que determinam a frequência de calibração é o tipo de instrumento de pressão utilizado. Diferentes instrumentos têm diferentes níveis de sensibilidade e precisão, o que pode afetar a necessidade de calibração. Por exemplo, manômetros de alta precisão podem exigir calibrações mais frequentes do que manômetros de uso geral. Além disso, instrumentos que operam em condições extremas, como altas temperaturas ou pressões, podem sofrer desgastes mais rapidamente e, portanto, necessitar de calibrações mais frequentes.
Outro fator a ser considerado é a aplicação do instrumento. Em ambientes industriais onde a segurança é uma preocupação primordial, como em indústrias químicas ou petroquímicas, a calibração deve ser realizada com mais frequência. Isso se deve ao fato de que leituras imprecisas podem levar a falhas catastróficas, colocando em risco a vida dos trabalhadores e causando danos ao meio ambiente. Portanto, em aplicações críticas, recomenda-se que a calibração seja realizada pelo menos uma vez por ano, ou até mesmo com mais frequência, dependendo das condições de operação.
Além disso, a frequência de calibração pode ser influenciada pela intensidade de uso do instrumento. Instrumentos que são utilizados continuamente ou em ciclos frequentes podem exigir calibrações mais regulares. Por outro lado, instrumentos que são utilizados esporadicamente podem ter intervalos de calibração mais longos. É importante monitorar o desempenho do instrumento e realizar calibrações sempre que houver suspeitas de que a precisão possa ter sido comprometida.
As diretrizes de calibração também podem ser influenciadas por normas e regulamentos da indústria. Muitas indústrias operam sob padrões rigorosos que exigem calibrações regulares para garantir a conformidade com as normas de segurança e qualidade. Por exemplo, a ISO 9001, uma norma internacional de gestão da qualidade, recomenda que as medições sejam realizadas com instrumentos calibrados e que a frequência de calibração seja determinada com base em critérios específicos. Portanto, é fundamental que as empresas estejam cientes das normas aplicáveis ao seu setor e sigam as diretrizes estabelecidas.
Além das diretrizes da indústria, as recomendações do fabricante do instrumento também devem ser levadas em consideração. Os fabricantes geralmente fornecem orientações sobre a frequência de calibração com base em testes e análises de desempenho. Essas recomendações são baseadas em dados coletados durante o desenvolvimento do instrumento e podem variar de acordo com o modelo e a aplicação. Portanto, é aconselhável consultar o manual do fabricante e seguir suas orientações para garantir a precisão e a confiabilidade do instrumento.
Outra prática recomendada é a realização de calibrações periódicas, mesmo que não haja sinais visíveis de falha. Isso é especialmente importante em ambientes onde a precisão é crítica. A calibração preventiva ajuda a identificar problemas antes que eles se tornem críticos, garantindo que os instrumentos estejam sempre operando dentro das especificações. A implementação de um programa de calibração regular pode ajudar a evitar interrupções na produção e a garantir a segurança dos processos.
Para empresas que não possuem recursos internos para realizar calibrações, a contratação de um Laboratório de Calibração especializado pode ser uma solução eficaz. Esses laboratórios oferecem serviços de calibração de alta qualidade, utilizando equipamentos de última geração e profissionais qualificados. A terceirização da calibração pode garantir que os instrumentos sejam calibrados de acordo com as normas e padrões da indústria, proporcionando tranquilidade e segurança.
Em resumo, a frequência recomendada para a calibração de instrumentos de pressão depende de vários fatores, incluindo o tipo de instrumento, a aplicação, a intensidade de uso e as diretrizes da indústria. A calibração regular é essencial para garantir a precisão e a confiabilidade das medições, especialmente em ambientes críticos. As empresas devem estar cientes das recomendações do fabricante e das normas aplicáveis ao seu setor, implementando um programa de calibração que atenda às suas necessidades específicas. A calibração preventiva e a contratação de laboratórios especializados podem ajudar a garantir que os instrumentos estejam sempre operando dentro das especificações, contribuindo para a segurança e a eficiência dos processos industriais.
Erros Comuns na Calibração e Como Evitá-los
A calibração de instrumentos de pressão é um processo crítico que garante a precisão e a confiabilidade das medições em diversas aplicações industriais. No entanto, existem erros comuns que podem ocorrer durante a calibração, comprometendo a eficácia do processo e resultando em medições imprecisas. Neste artigo, discutiremos alguns dos erros mais frequentes na calibração de instrumentos de pressão e como evitá-los para garantir resultados confiáveis.
Um dos erros mais comuns na calibração é a falta de um padrão de referência adequado. A calibração deve ser realizada em comparação com um instrumento de referência que tenha uma precisão superior. Se o padrão de referência não for calibrado ou não atender às especificações necessárias, as medições do instrumento em teste podem ser comprometidas. Para evitar esse erro, é fundamental utilizar padrões de referência que sejam rastreáveis a laboratórios acreditados e que estejam dentro do período de validade de calibração.
Outro erro frequente é a calibração em condições inadequadas. A temperatura, a umidade e a pressão atmosférica podem afetar as medições de pressão. Se a calibração for realizada em condições que não correspondem ao ambiente de operação do instrumento, os resultados podem ser imprecisos. Para evitar esse problema, é importante realizar a calibração em um ambiente controlado, onde as condições sejam mantidas dentro dos limites especificados pelo fabricante do instrumento. Além disso, é recomendável que a calibração seja realizada em um local que minimize a interferência de vibrações e campos eletromagnéticos.
A falta de treinamento adequado dos operadores também é um fator que contribui para erros na calibração. Operadores não treinados podem não seguir os procedimentos corretos, resultando em medições imprecisas. Para evitar esse erro, as empresas devem investir em treinamento contínuo para suas equipes, garantindo que todos os operadores estejam familiarizados com os procedimentos de calibração e com o funcionamento dos instrumentos. A documentação clara e acessível dos procedimentos de calibração também pode ajudar a minimizar erros.
Outro erro comum é a calibração em intervalos inadequados. A frequência de calibração deve ser determinada com base em vários fatores, incluindo o tipo de instrumento, a aplicação e as condições de operação. Se a calibração for realizada com muita frequência, pode resultar em custos desnecessários, enquanto calibrações realizadas com pouca frequência podem levar a medições imprecisas. Para evitar esse problema, as empresas devem estabelecer um cronograma de calibração baseado em diretrizes do fabricante, normas da indústria e histórico de desempenho do instrumento.
Além disso, a falta de documentação adequada durante o processo de calibração pode levar a erros. É essencial registrar todas as medições, ajustes e resultados da calibração para garantir a rastreabilidade e a conformidade. A documentação adequada também facilita a identificação de tendências e problemas recorrentes, permitindo que as empresas tomem medidas corretivas quando necessário. Para evitar esse erro, as empresas devem implementar um sistema de gerenciamento de documentos que inclua registros de calibração e procedimentos operacionais padrão.
Outro erro que pode ocorrer é a utilização de equipamentos de calibração inadequados. O uso de instrumentos que não são apropriados para a faixa de pressão do instrumento em teste pode resultar em medições imprecisas. Para evitar esse problema, é importante garantir que todos os equipamentos de calibração estejam calibrados e em boas condições de funcionamento. Além disso, os operadores devem estar cientes das especificações dos instrumentos de calibração e utilizá-los de acordo com as recomendações do fabricante.
A calibração de instrumentos de pressão também pode ser afetada por erros de interpretação dos resultados. Os operadores podem interpretar incorretamente os dados de calibração, levando a ajustes inadequados no instrumento. Para evitar esse erro, é fundamental que os operadores sejam treinados para entender os resultados da calibração e como eles se relacionam com as especificações do instrumento. A utilização de gráficos e tabelas de referência pode ajudar na interpretação dos dados e na identificação de desvios.
Além disso, a falta de manutenção preventiva nos instrumentos de pressão pode levar a erros de calibração. Instrumentos que não são mantidos adequadamente podem apresentar desgastes e falhas que afetam a precisão das medições. Para evitar esse problema, as empresas devem implementar um programa de manutenção preventiva que inclua inspeções regulares e reparos conforme necessário. A manutenção adequada ajuda a garantir que os instrumentos estejam sempre em condições ideais de funcionamento.
Por fim, é importante mencionar que a calibração de instrumentos de pressão, como o Medidor de vazão ultrassônico , deve ser realizada por profissionais qualificados e experientes. A calibração é um processo técnico que requer conhecimento especializado, e a falta de experiência pode resultar em erros significativos. Portanto, as empresas devem considerar a contratação de serviços de calibração de laboratórios acreditados para garantir a precisão e a confiabilidade das medições.
Em resumo, a calibração de instrumentos de pressão é um processo crítico que pode ser afetado por diversos erros comuns. A falta de um padrão de referência adequado, condições inadequadas, falta de treinamento, calibrações em intervalos inadequados, documentação insuficiente, uso de equipamentos inadequados, erros de interpretação, falta de manutenção e falta de experiência são alguns dos principais fatores que podem comprometer a eficácia da calibração. Ao identificar e abordar esses erros, as empresas podem garantir medições precisas e confiáveis, contribuindo para a segurança e a eficiência de seus processos industriais.
Em conclusão, a calibração de instrumentos de pressão é uma prática indispensável para assegurar a precisão e a confiabilidade das medições em ambientes industriais e laboratoriais. A compreensão dos métodos de calibração, a definição de uma frequência adequada e a identificação de erros comuns são aspectos cruciais que contribuem para a eficiência e a segurança dos processos. Ao implementar práticas de calibração rigorosas e seguir as diretrizes recomendadas, as empresas podem não apenas garantir a conformidade com normas e regulamentos, mas também otimizar a qualidade de seus produtos e serviços. Investir em calibração é, portanto, um passo essencial para promover a excelência operacional e a segurança em qualquer setor.